Mars Power Solutions specialize in high-efficiency plastic processing equipment, including advanced injection molding machines, precision-engineered hoppers, intelligent PLC control systems, robust crushers, and energy-saving servo systems. Our injection molding machines are designed for consistent, high-speed performance with the flexibility to handle various materials and complex part geometries. Paired with our high-capacity hoppers, material flow is optimized to reduce downtime and ensure continuous operation. At the heart of our equipment, PLC systems provide accurate, user-friendly control, allowing for precise adjustments and enhanced productivity. Our crushers are built to handle plastic waste efficiently, enabling easy recycling and minimal waste generation. The integrated servo systems enhance machine responsiveness and significantly reduce energy consumption, offering a sustainable solution to manufacturing needs. Mars Power Solutions is committed to delivering innovative machinery that drives productivity and sustainability in the plastic industry.
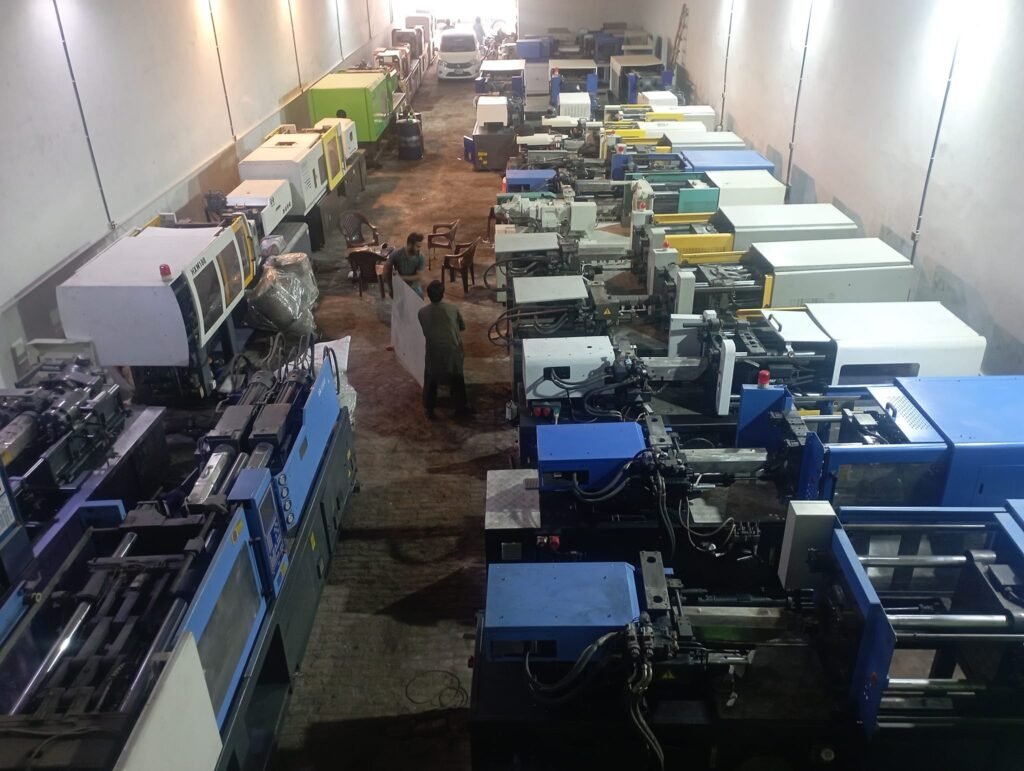
Injection Molding Machines Parts
PLC (Programmable Logic Controller):
Acts as the brain of the machine, controlling all operations such as clamping, injection, cooling, and ejection. It ensures accurate timing and sequence of processes.PLC Card:
A modular part of the PLC system that facilitates communication between the machine’s sensors and actuators, ensuring seamless execution of programmed tasks.Hopper:
A funnel-shaped container that holds and feeds plastic granules into the barrel. It can be fitted with a dryer to remove moisture from the raw material.Crusher:
Located near the machine, it recycles defective or excess plastic parts by grinding them into smaller pieces, which can be reused in the manufacturing process.Mold Clump (Clamping Unit):
Holds the mold securely in place during the injection process and provides the necessary force to keep it closed, preventing material leakage.Servo System:
An energy-efficient motor system that controls the speed, pressure, and position of the machine components with precision, contributing to reduced energy consumption and better product quality.Connectors:
Facilitate the integration of various electrical and hydraulic components, ensuring smooth communication between the machine’s systems.
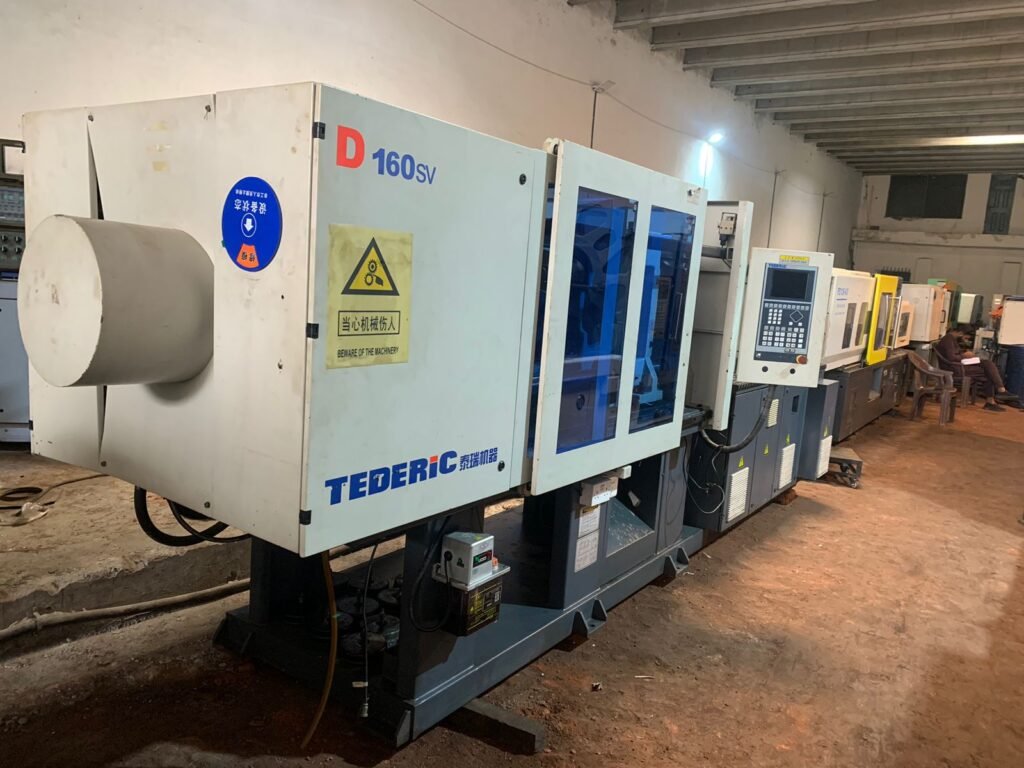
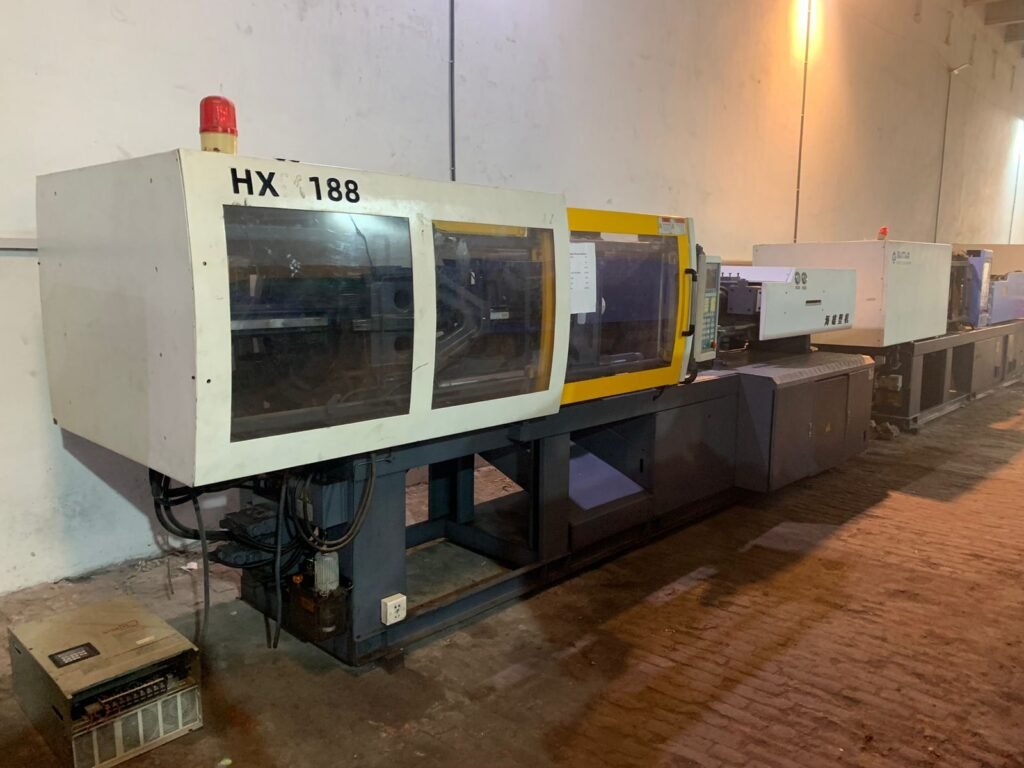
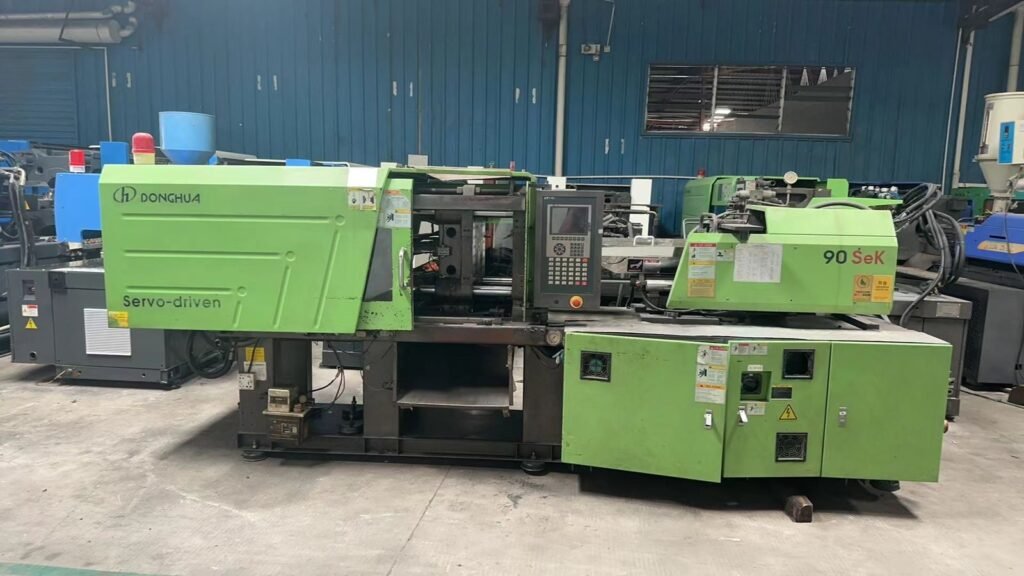
SEK 90-ton injection molding machines are versatile and efficient tools for producing high-precision plastic components in various industries, including automotive, medical, and consumer goods. With a clamping force of 90 tons, these machines excel at handling medium-sized molds, offering superior accuracy and repeatability. They often feature advanced control systems for precise temperature, pressure, and cycle time management, ensuring consistent quality in production. Additionally, their energy-efficient designs and customizable options make them attractive for manufacturers seeking cost-effective and sustainable solutions. This balance of performance and adaptability positions the SEK 90-ton machines as a reliable asset in modern manufacturing processes.